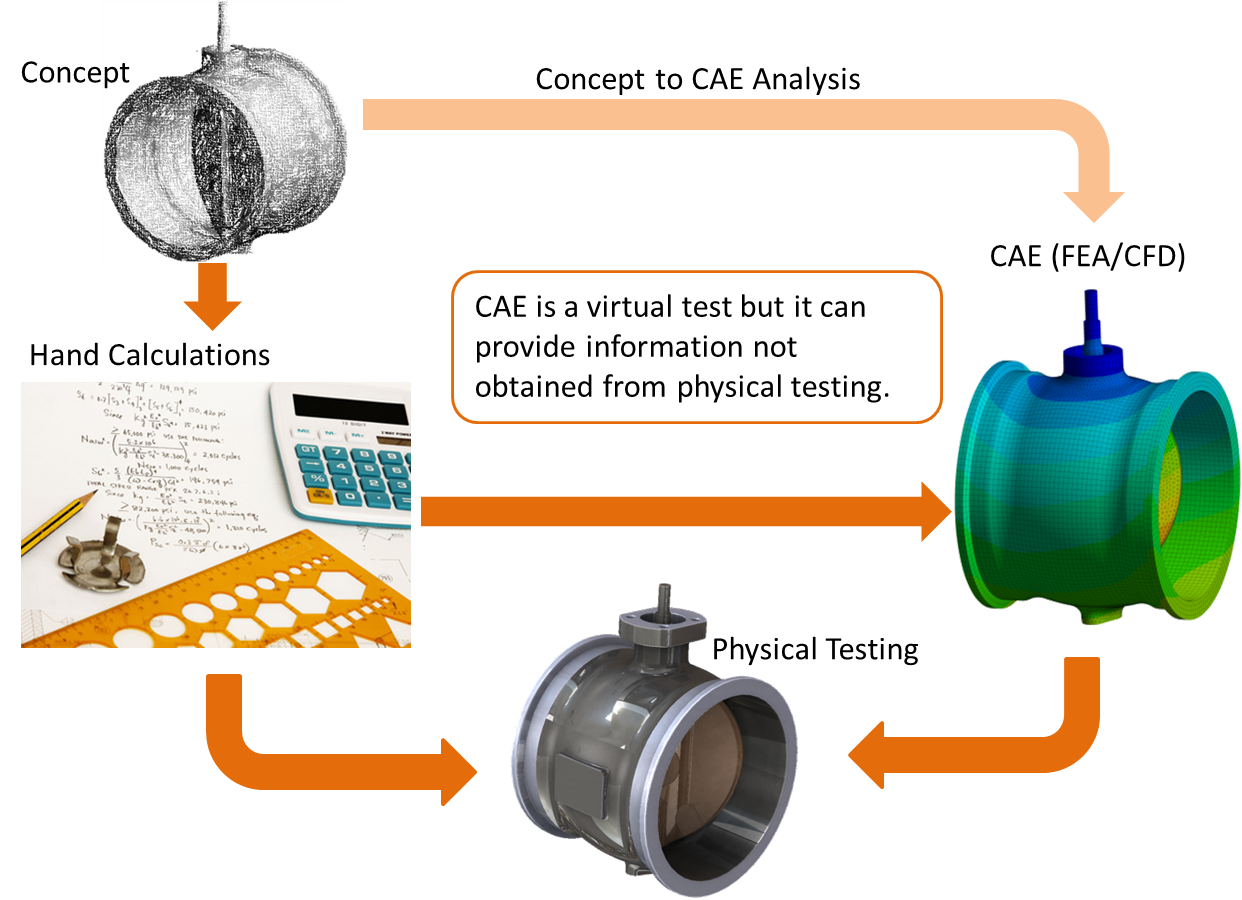
Role of Computer-Aided Engineering (CAE) in Modern Engineering
Finite Element Analysis (FEA)
Advanced simulations based on numerical computations such as the finite element method (FEM) and computational fluid dynamics (CFD) are an essential part of the product development process. This capability enables virtual prototyping and testing which significantly cuts down product development time and cost. We provide a full spectrum of numerical simulations, however, not every aspect of real-world physics can or should be modeled on a computer. In some cases, simple analytical models might be sufficient, on the other hand, experiments using physical prototype might be needed. Please consult with us to establish the right approach for your specific application. We offer the following capabilities:
General Structural Analysis
- Structural – Thermal FE Analysis
- Thermal Structural Coupled Analysis.
- Joints: Bolted, Adhesive (bonded), Welded, Riveted.
- Nonlinear Plasticity & Buckling.
- Fatigue and Fracture Analysis.
- Composite Structures.
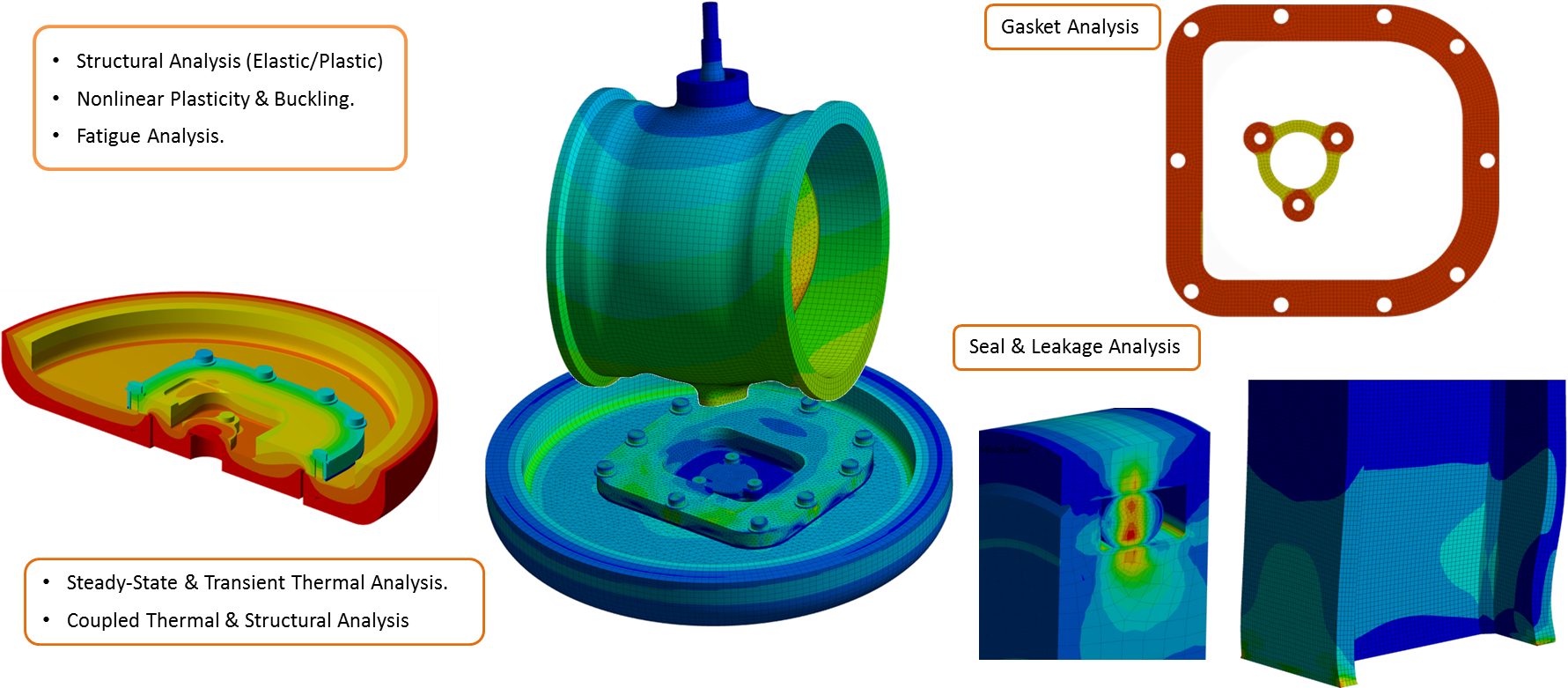
Multi-body and Structural Dynamics
- Rigid Body Dynamics
- Flexible body Dynamics
- Simulation of Mechanisms and Machines.
- Mechanical Vibrations: Modal & Harmonic, Random Vibration Analysis.
- Transient Dynamics.
- Response Spectrum Analysis.
- Aeroelastic Analysis.
- Impact Dynamics
Rotor Dynamics
- Critical speed analysis.
- Rotor stability predictions.
- Unbalanced Response.
- Transient speed ramp up and ramp down simulations.
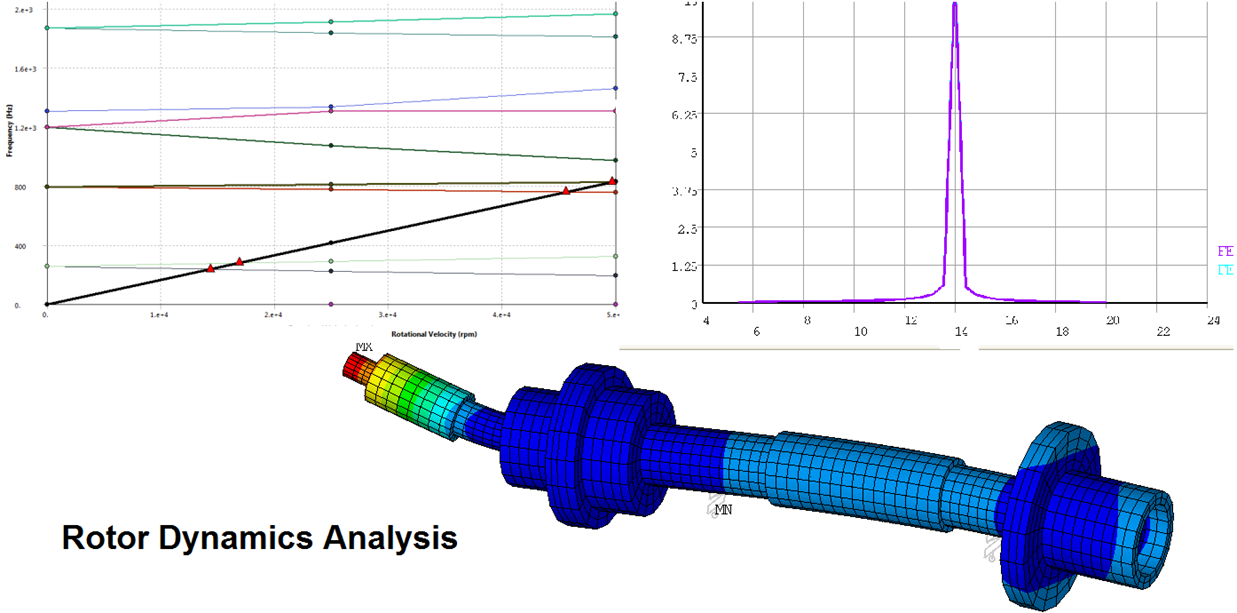
Structural Topology Optimization
We have the capability to optimize structural designs to reduce mass, deflections as well as change structural stiffness to improve mechanical vibration behavior. Various tools and methods are utilized such as topology and shape optimization. Additionally, any aspect of thermal-structural performance can also be optimized
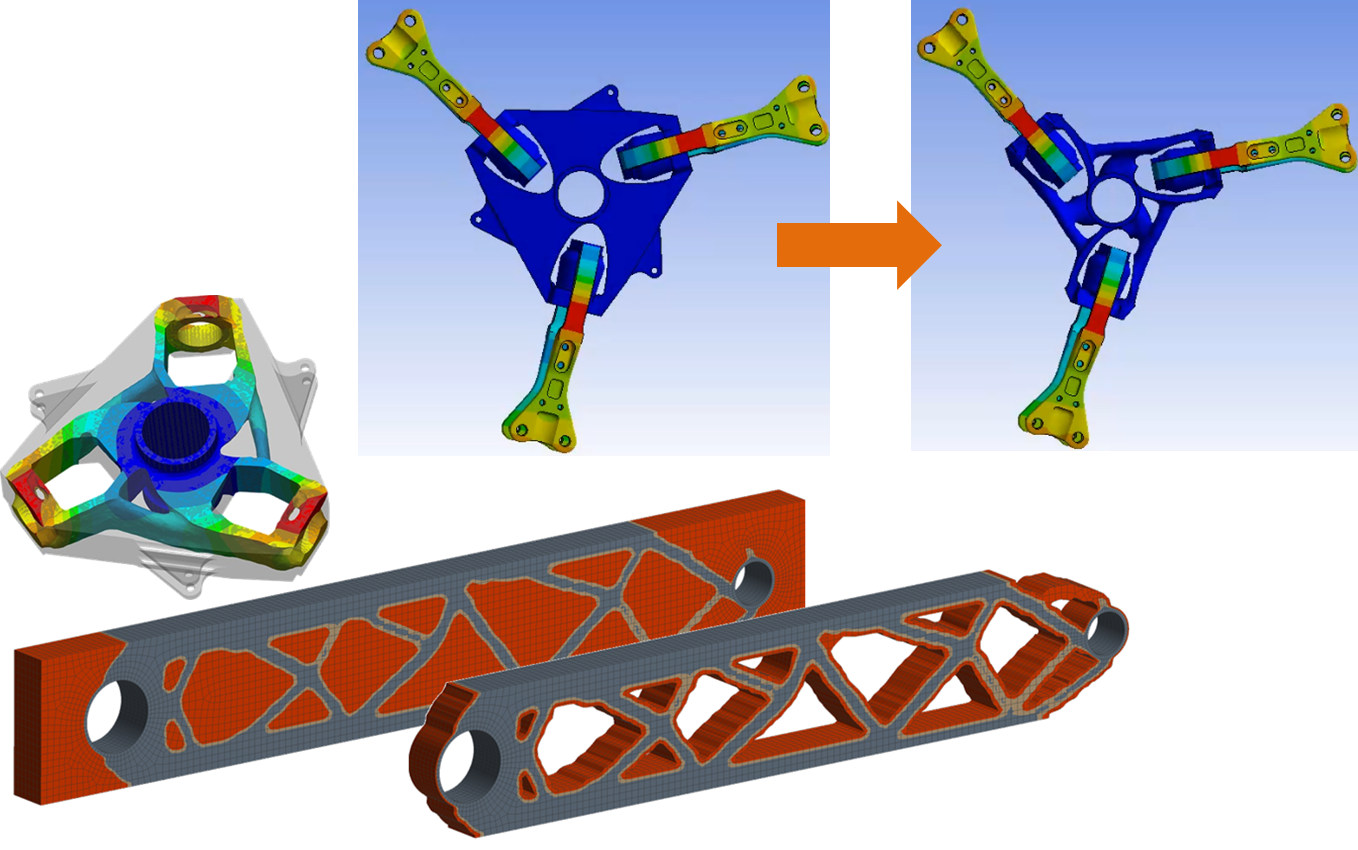
Analytical Spread Sheet & FEA Tools
We provide a full spectrum of numerical simulations, however, not every aspect of real-world physics can or should be modeled and numerically computed. On the other hand, physical experiments using test rigs might be needed. In some cases, simple analytical spreadsheet models are sufficient for quick design assessment, concept evaluation, etc.
- We have developed in house analytical tools for analysis such as bolted joints, gaskets, and flanges based on current and established design and analysis methods.
- We also have the capability to link spreadsheet tools with finite element analysis using ANSYS APDL. This standardizes analysis and removes any dependence on the user skill level. All post-processing can be automated.
- Based on your product development needs, we can custom build simple analytical spreadsheet tools for your organization.
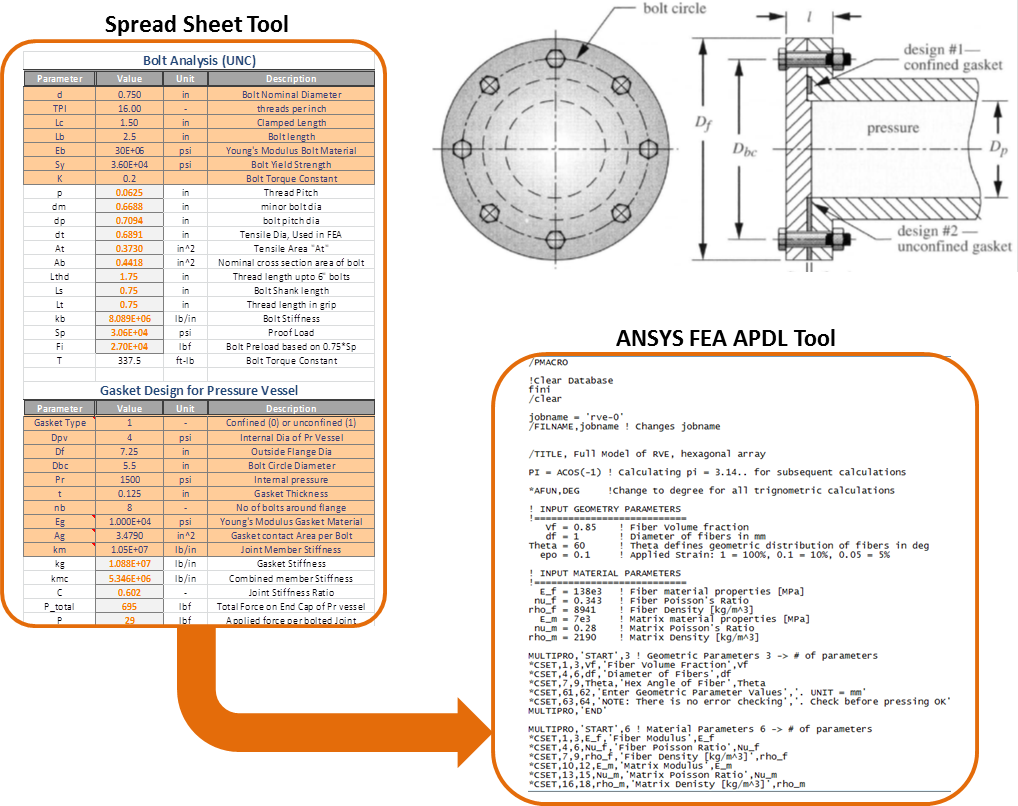
Composite Material Structures
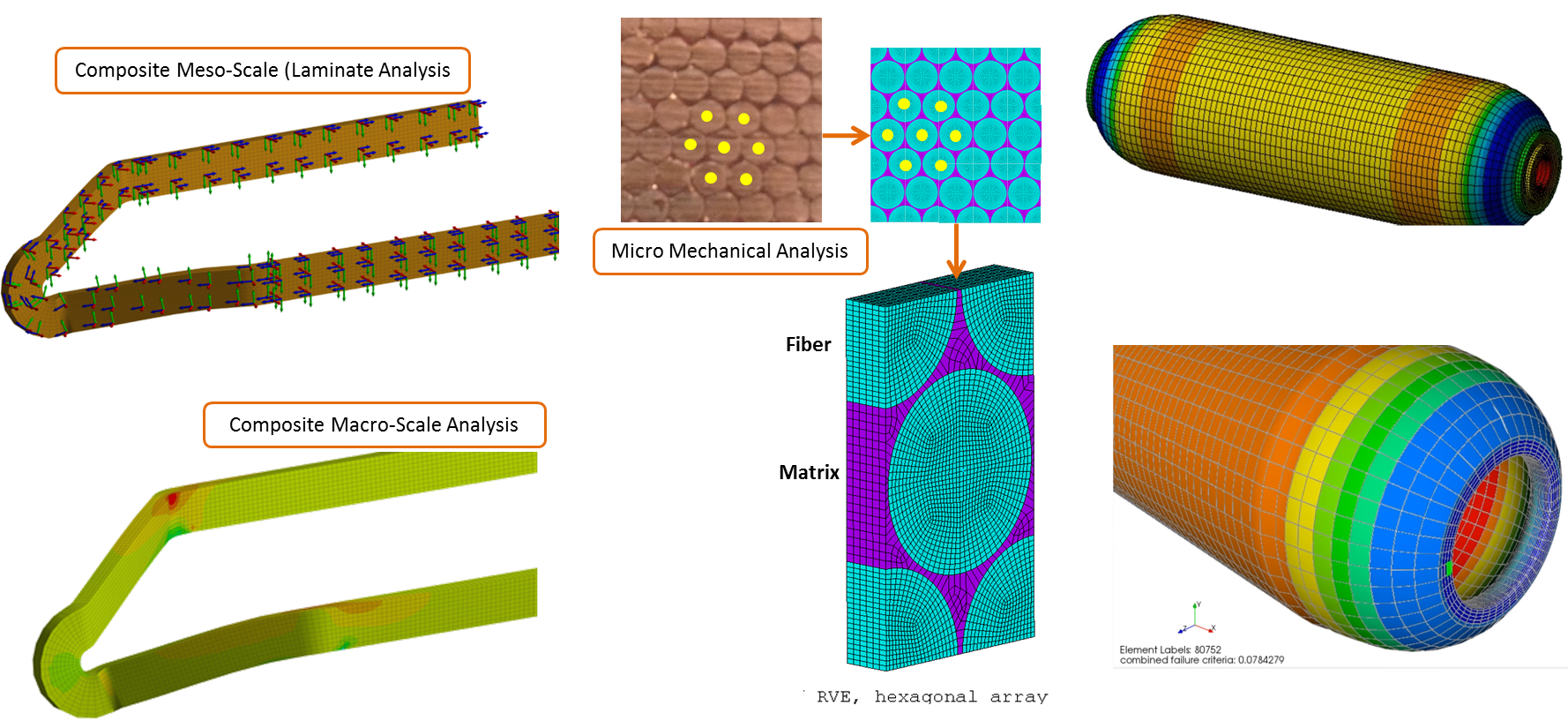